Knuckle Joint in Cars: Function and Applications
Knuckle Joint in Cars: Function and Applications
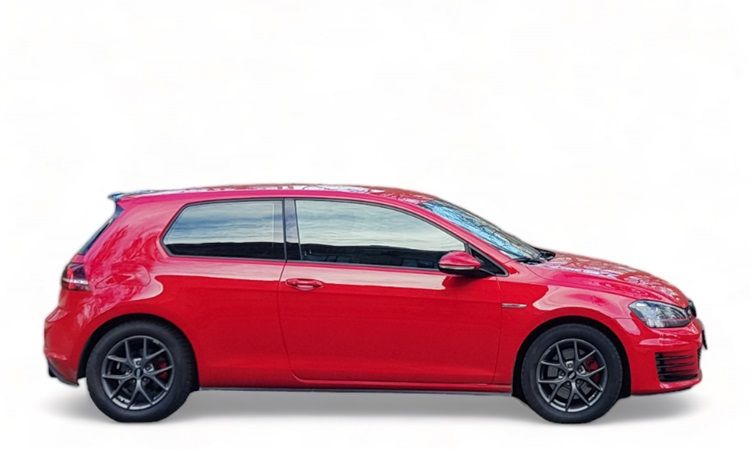
A knuckle joint in cars is the fundamental component that connects the steering wheel to the suspension system and front wheels. It is designed to provide strength and directional assistance in automobiles. Knuckle joints are essential for safe driving because a broken one can cause a vehicle to lose control and cause accidents. Along with proper maintenance of mechanical parts of the automobile, having car insurance is also essential to safeguard your ride.
Knuckle Joint Parts
The knuckle joint comprises various interconnected parts, each designed for a specific purpose. Here is an in-depth look at its primary components:
1. Fork End
The fork end forms the dual-arm structure of the knuckle joint. Its primary function is to securely hold the knuckle pin and the eye end in position. This capability supports angular movement, which is crucial for systems requiring flexibility under load.
2. Eye End
The eye end complements the fork end by forming a single-eye structure that connects seamlessly with the double-eye fork end. When paired with the knuckle pin, this component facilitates smooth articulation. Its design ensures that the joint distributes the load evenly, preventing stress concentrations that could lead to failures.
3. Knuckle Pin
The knuckle pin is the central component, acting as the backbone of the joint. This cylindrical pin locks the fork, and eye ends together while bearing the bulk of the load. It allows the joint to swivel, supporting smooth relative motion. The knuckle pin is typically made from high-strength materials like alloy steel to handle wear and tear. This enhances its ability to withstand heavy loads and high-pressure conditions.
4. Collar and Taper Pin
The collar keeps the knuckle pin in place during operation, while the taper pin provides additional security by locking the collar. Together, these components ensure the assembly remains secure, even under heavy loads. This added layer of security also safeguards the joint from accidental disassembly during use.
5. Bush
The bush acts as a protective lining between the knuckle pin and the joint's internal surfaces. By reducing friction, it minimises wear and enhances the joint's performance. This component is essential for extending the operational lifespan of the joint, ensuring smooth functioning over time.
What is the Design Procedure for Knuckle Joint?
Designing a knuckle joint requires a systematic approach to ensure it can withstand the forces it will encounter. Here’s how it’s done:
1. Material Selection
Engineers typically use high-grade steel or alloys with excellent tensile, compressive, and shear properties.
2. Load Assessment
Calculating the tensile, compressive, and shear forces helps determine the required dimensions of the joint components.
3. Determining Rod Diameter
Engineers determine the diameter based on the maximum expected tension the rod will experience. The material’s tensile strength is a key factor, as it must withstand the forces without deforming or failing. The rod's size is finalised to ensure safe and efficient load transfer, balancing durability and material economy.
4. Designing Eye and Fork Ends
The eye and fork ends are carefully crafted to resist tensile and shear forces.
• Eye End
The eye end's thickness and dimensions are calculated to handle the applied tensile stress. It is designed to fit snugly with the knuckle pin while evenly distributing the load. Proper material selection and dimensions allow it to withstand high loads without risk of failure.
• Fork End
The fork end features two arms to hold the pin and eye end for smooth motion securely. Its dimensions are optimised to resist shear forces and provide structural stability.
5. Knuckle Pin Design
The knuckle pin is the central element of the joint, and it must withstand both shear and bending stresses.
• Shear Resistance
The pin’s diameter is chosen to resist shear stress caused by the applied load. The material is selected for its strength and resilience, typically high-grade steel or similar alloys.
• Bending Resistance
The pin's design is also tested against bending stresses to prevent deformation under load. Its dimensions are optimised for durability, ensuring it can handle rotational and dynamic forces
6. Incorporating Safety Factors
A safety factor is added to account for uncertainties, such as unexpected loads or material inconsistencies. This makes the design more robust and reliable. Although this ensures safety, having valid comprehensive car insurance can enhance protection and help you financially during unfortunate accidents.
7. Validating the Design
Engineers validate the design by simulating real-world conditions, including maximum load scenarios. This step ensures that the knuckle joint can perform safely and effectively under varying circumstances.
8. Manufacturing and Testing
After finalising the design, the joint is manufactured using precision techniques. Rigorous testing follows to confirm the joint meets all safety and performance standards.
Applications of Knuckle Joints in Cars
Knuckle joints are extensively used in automobiles due to their ability to provide flexibility while maintaining structural integrity. Some common automotive applications include:
1. Suspension Systems
Knuckle joints connect the control arms, enabling angular movement. This allows the suspension to adapt seamlessly to road irregularities. As a result, ride comfort and vehicle stability improve, particularly during turns and over uneven terrain.
2. Steering Mechanisms
Knuckle joints play a key role in transmitting motion with precision in steering systems. Their flexibility supports efficient directional changes, improving manoeuvrability. They ensure the driver’s input is accurately translated into wheel movement, which is crucial for safe and responsive steering.
3. Brake Systems
Knuckle joints are used in brake linkages to ensure reliable motion transfer, balancing rigidity and flexibility for optimal brake performance.
4. Transmission Linkages
Knuckle joints facilitate smooth power transfer in vehicle transmission systems. They connect various components, enabling uninterrupted motion while accommodating small misalignments. This ensures efficient power delivery and maintains the performance of the transmission system under dynamic conditions.
Conclusion
The knuckle joint is a critical component, enabling flexibility and strength in automotive systems. Well-designed knuckle joints in cars support its performance for the long haul. Similarly, car insurance is a long-term investment that shields you from unforeseen costs. Protecting your vehicle with comprehensive third-party car insurance ensures peace of mind and safeguards against unforeseen expenses.
Disclaimer: The above information is for illustrative purposes only. For more details, please refer to the policy wordings and prospectus before concluding the sales.
RELATED ARTICLES
What Are the Different Types of Car Rims?
How to Get Spare Car Keys Easily in India?
Understanding the Tyre Size of Your Vehicle
Front-Wheel Drive Vs. Rear-Wheel Drive
Electric Steering vs Hydraulic Steering: Key Differences